The oxide quality is better if anodizing is carried out by using a pulse rectifier, the average current of which is equal to the one of a conventional rectifier. This advantage is proved by several tests and can also theoretically be explained.
Time savingExperience shows that by using a pulsating waveform it is possible to carry out anodizing (and also other electrodeposition treatments) at a higher average current in comparison with conventional direct current.
This may well be due to the cooling of the oxide layer in the interval between two consecutive pulses, following the known “recovery” theory.
Therefore by using pulse rectifiers it is possible to get the same thickness in shorter time, with the benefits of 20-25% approx. time saving.
Comparison of pulse and conventional rectifiers (same average current density)
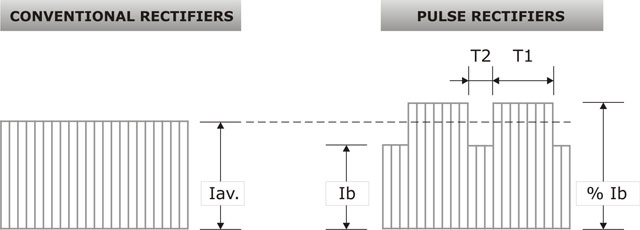
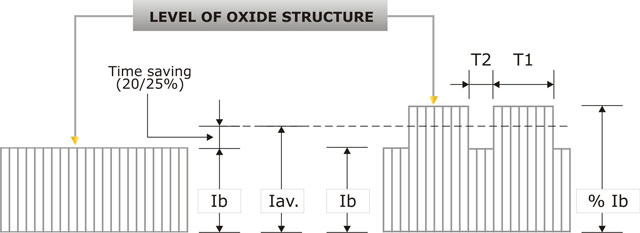
Theoretical explanation
The accepted recommended current density range for anodic oxidation of aluminium lies between 1.4 and 1.8 A/dm2.
When using too low a value of current density this gives a very porous layer of oxide film which results in an excessively wet surface, this is therefore more susceptible to the “re-attack” of the electrolytes.
In addition, a low current density also requires a longer oxidation time to obtain a given oxide film which creates an even greater dissolution of the oxide being formed.
Conversely, if the current density increases, the time required to produce the same given oxide film will be decreased and moreover the hardness and corrosion/abrasion resistance will be increased.
When considering these factors, it is clearly better to carry out the oxidation at a sufficiently high value of current density, within certain limits of course that the heat generated can be easily dissipated to prevent damage to the oxide layer by burning or perforation etc.
The use of pulse rectifiers in anodizing gives the advantages of using a high current density without the disadvantage of excessive heat generation and the consequent detrimental effects to the oxide film.
Infact, if we compare the waveform of a conventional rectifier with that of the pulse rectifier, the oxide quality achieved is the relative to the higher current level and not the average value, upon which the heat generation depends
This can be explained theoretically by the following considerations:
- The pulse duration at the high level (T1) is longer than the low level duration (base) T2
- Due to a “recovery phenomenon” at the time of the fast change from high to low level, the modification of the oxide happens in such a slow way that it prevents any significant changes.